A real housing solution for residents of the Katrina-battered Gulf
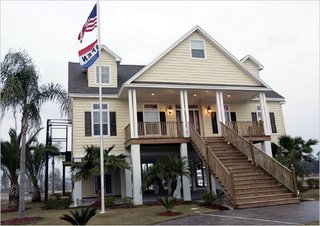
Most developers who proposed building modular homes was not warmly received by the community's low-income residents back then. The reigning conventional wisdom was that modular (pre-fab) housing was inferior to stick-built structures After years of hard work and political battles leading up to the historic revitalization plan for the neighborhood, these proud and empowered residents were not going to settle for second-rate "mass-manufactured" houses.
During the four years I spent at DSNI, I saw attitudes towards modular housing slowly change. When residents understood that modular wasn't necessarily synonymous with cookie-cutter development and that this technique could result in tighter, more energy efficiency homes, they were more willing to consider them as part of their housing stock. (GW)
Katrina Victims Find A Solution: Modular House
By Leslie Eaton
New York Times
January 6, 2007
PASS CHRISTIAN, Miss. — Of the hundreds of houses swept away by Hurricane Katrina in this small Gulf Coast town, only a fraction have been replaced. The price of building materials has skyrocketed, and the services of even mediocre contractors can be hard to come by.
But on East North Street recently, a swarm of workmen put the final touches on Gwen and Rudy Cardreon’s new home, a tan ranch house that sprang up, on 11-foot piling, in a matter of days. Constructed in three pieces in a factory hundreds of miles away, the house came equipped with carpets, curtains, even ceiling fans, but looks as if it were custom built in the Cardreons’ yard.
“Isn’t it gorgeous?” Mrs. Cardreon exclaimed, standing in her new kitchen as construction workers hammered on the wooden staircase outside.
Before the August 2005 hurricane, so-called modular houses like the Cardreons’ were almost unknown in Mississippi, where houses tended to be the traditional “stick built” on site or mobile homes. Modulars have been popular until now mainly in Northern states with short building seasons and high labor costs.
But since the storm, modular houses, which range from simple shotgun-style cottages to fancy mini-mansions, are starting to appear across the Gulf Coast, as public officials and private citizens search for ways to speed the slow pace of recovery and begin experimenting with new forms of shelter.
Modular houses have a number of advantages over conventionally built houses, their advocates said. For example, once they are delivered, modular homes can sometimes be completed in days, rather than months. They are relatively easy to perch up on stilts to comply with flood zone rules. They require less local labor in a region where there is more than enough construction work to go around. Some are less expensive than conventional houses — they range from $50,000 to $500,000 — and manufacturers say some can withstand 160-mile-an-hour winds.
The number of modular houses on the Gulf Coast is still small; perhaps 400 have been installed in Mississippi in the last year, said Fred C. Hallahan, a consultant in Baltimore who tracks the modular business.
But Mr. Hallahan and other experts expect the trickle of modular housing to grow rapidly this year, and perhaps lead to even bigger changes.
“Really, if we look back 20 years from now, we could see a dramatic shift in the way houses get built,” said David W. Hinson, a professor of architecture at Auburn University in Alabama.
In Mississippi, Hurricane Katrina destroyed 70,000 houses and apartments, according to state estimates; more than 30,000 families in the state still live in the small trailers supplied by the Federal Emergency Management Agency.
Though Mississippi is widely considered to be far ahead of Louisiana in terms of recovery, only 2,480 building permits had been issued by the end of November for new home construction in the hardest-hit counties along the coast, according to the governor’s office.
Officials cite many reasons for the slow going, including insurance issues, wetlands regulations, permit backlogs and infrastructure problems. And, of course, money: many people are still fighting with their insurance companies, and over the summer, Mississippi’s grant program to help homeowners rebuild ran into some of the same bottlenecks that still plague Louisiana’s Road Home program.
But after several adjustments, the Mississippi program has distributed more than $500 million to more than 8,000 homeowners, said Donna Sanford, who supervises the program for the Mississippi Development Authority. Last month, the federal Department of Housing and Urban Development approved a second phase of the program, to help low-income applicants and those who lived in the flood zones.
With the prospect of money finally starting to flow to housing, experiments are going on across the Gulf Coast as people look for ways to build more quickly, more cheaply and with more resistance to hurricanes.
Builders are exploring houses made of steel or concrete, and are considering putting housing above stores, as they do in concentrated urban areas like New York City. Volunteer groups have been ordering house-in-a-box kits from New Hope Construction, a nonprofit supplier in Tennessee that often works closely with churches.
Lowe’s, the big building supply chain, says it will be selling everything necessary to build a Katrina Cottage, designed as a low-cost, high-quality alternative to trailers.
[Directed by Congress, even FEMA has gotten into the act, awarding about $400 million on Dec. 22 to various state-sponsored pilot programs to replace its travel trailers with roomier and sturdier housing.]
But the big push seems to be modular housing, which is being used not just by private developers, but also by Habitat for Humanity and Catholic Charities in New Orleans.
“It’s the only answer, it is simply the only answer in Mississippi,” said Fred Carl Jr., the founder of the Viking Range Corporation, who served as the Hurricane Katrina housing coordinator for Gov. Haley Barbour.
Mr. Carl said he was trying to lure a major modular manufacturer to the state. “We need nine or ten thousand houses a year,” he said.
There is already one home-grown modular builder in Mississippi, Safeway Homes, which Buddy Jenkins and his brother started in 2005. “We’re really a stick-built house moved in component parts,” Mr. Jenkins said of his tidy houses, which are rated to withstand high winds.
At the company’s spotless plant in Lexington, a small town north of the state capital, Jackson, Joel E. Smith walks a visitor through the 16 stations where the houses are framed and insulated by about 100 workers. The ducts and plumbing are installed, fixtures added, doors and windows placed, and each half of a house is tightly screwed and glued.
Once they are delivered, a crane will lower the halves onto a foundation, where they will be joined, and a roof, also built at the plant, will be attached. The basic house costs about $58,000, company officials said, but the final cost will depend on the land, the foundation, the developer and whether the owner has chosen any extras like arched windows.
Safeway Homes has built about 250 houses, Mr. Smith said, and could make as many as three a day. But there are hurdles. Some are regulatory; building inspectors are often unfamiliar with modular housing, and customers must buy through a developer rather than from manufacturers. And some consumers still equate modular houses with mobile homes, in part because they are sold by many of the same manufacturers. That image problem is being tackled by Victor Planetta, a developer based in Louisiana who, with his son, Victor Jr., has started putting modular houses in their Mississippi developments.
Their showplace, on the main highway into Bay St. Louis, near Pass Christian, is a bright yellow, two-story house on pillars with a fountain burbling out front and a big motorboat named Beyond Belief out back in the canal.
The house, which was trucked in several pieces from a Genesis Homes plant in Lake City, Fla., and assembled on the site, has crown moldings, granite, silk flowers and tassels; there is even an elevator. More than 1,000 people have visited the house, which will sell for about $425,000, the Planettas said.
Here in the Pass, as the devastated town is known, about three dozen simple modular houses, including Gwen and Rudy Cardreon’s, have been installed though a program called Home Again. Phil Eide, who runs the program for ECD/Hope, a community development organization, said that modular housing had been harder to deal with than he had first hoped. For example, it takes 41 steps to get a permit, he said, and some suppliers make promises they do not keep.
But the program has attracted backing from James L. Barksdale, the former Internet executive and investor who served as chairman of Mississippi’s Commission on Recovery, Rebuilding and Renewal, who just bought about 35 modular houses that Home Again will place in communities.
Mr. Barksdale said he had become frustrated with the lack of progress in returning affordable housing to the Gulf Coast.
“My goal,” he said, “is to prove to people that we can do this, and then let it become a lot bigger program.”
0 Comments:
Post a Comment
<< Home